某汽車零部件制造工廠擁有多條生產(chǎn)線,包括沖壓、焊接、涂裝和總裝等環(huán)節(jié),每個(gè)環(huán)節(jié)都配備了大量的生產(chǎn)設(shè)備,如壓力機(jī)、焊接機(jī)器人、噴涂設(shè)備和裝配線等。隨著市場競爭的加劇和客戶需求的多樣化,工廠面臨著生產(chǎn)效率提升、成本控制和質(zhì)量保證等多重挑戰(zhàn)。為了實(shí)現(xiàn)這些目標(biāo),工廠決定推進(jìn)數(shù)字化轉(zhuǎn)型,而車間設(shè)備數(shù)據(jù)采集則是其中的關(guān)鍵一環(huán)。
一、實(shí)際問題與需求
生產(chǎn)效率提升:需要實(shí)時(shí)監(jiān)控設(shè)備的運(yùn)行狀態(tài),及時(shí)發(fā)現(xiàn)并解決生產(chǎn)瓶頸,提高整體生產(chǎn)效率。
成本控制:通過數(shù)據(jù)分析,預(yù)測設(shè)備維護(hù)需求,減少非計(jì)劃停機(jī)時(shí)間,降低維護(hù)成本。
質(zhì)量保證:監(jiān)控生產(chǎn)過程中的關(guān)鍵參數(shù),確保產(chǎn)品質(zhì)量符合標(biāo)準(zhǔn),減少廢品率。
能源管理:實(shí)時(shí)監(jiān)測能源消耗,優(yōu)化能源使用策略,降低能耗成本。
二、解決方案
針對上述需求,我們提出了一套車間設(shè)備數(shù)據(jù)采集解決方案,該方案主要包括以下幾個(gè)部分:
1、傳感器與數(shù)據(jù)采集設(shè)備
在每臺關(guān)鍵設(shè)備上安裝傳感器,如溫度傳感器、振動(dòng)傳感器、電流傳感器等,實(shí)時(shí)監(jiān)測設(shè)備的運(yùn)行狀態(tài)和工作環(huán)境。
使用TDE數(shù)據(jù)采集網(wǎng)關(guān)收集傳感器的數(shù)據(jù),并通過有線或無線方式傳輸至數(shù)網(wǎng)星云平臺。
2、數(shù)據(jù)傳輸與存儲
建立穩(wěn)定的數(shù)據(jù)傳輸網(wǎng)絡(luò),確保采集到的數(shù)據(jù)能夠?qū)崟r(shí)、準(zhǔn)確地傳輸至數(shù)據(jù)中心。使用數(shù)據(jù)庫系統(tǒng)存儲數(shù)據(jù),便于后續(xù)的數(shù)據(jù)分析和處理。
3、數(shù)據(jù)分析與可視化
利用數(shù)網(wǎng)星云平臺對采集到的數(shù)據(jù)進(jìn)行處理和分析,提取有價(jià)值的信息。將分析結(jié)果以圖表、報(bào)表等形式展示給管理人員和操作人員,便于他們快速了解設(shè)備狀態(tài)和生產(chǎn)情況。
4、預(yù)警與報(bào)警系統(tǒng)
根據(jù)數(shù)據(jù)分析結(jié)果,設(shè)置預(yù)警和報(bào)警閾值。當(dāng)設(shè)備狀態(tài)或生產(chǎn)參數(shù)達(dá)到或超過閾值時(shí),系統(tǒng)自動(dòng)發(fā)出預(yù)警或報(bào)警信號,提醒相關(guān)人員及時(shí)采取措施。
5、維護(hù)管理系統(tǒng)
結(jié)合數(shù)據(jù)分析結(jié)果,制定設(shè)備維護(hù)計(jì)劃,包括定期維護(hù)、預(yù)防性維護(hù)和故障后維護(hù)等。
記錄每次維護(hù)的詳細(xì)信息,包括維護(hù)時(shí)間、維護(hù)人員、維護(hù)內(nèi)容等,便于后續(xù)的設(shè)備管理和維護(hù)優(yōu)化。
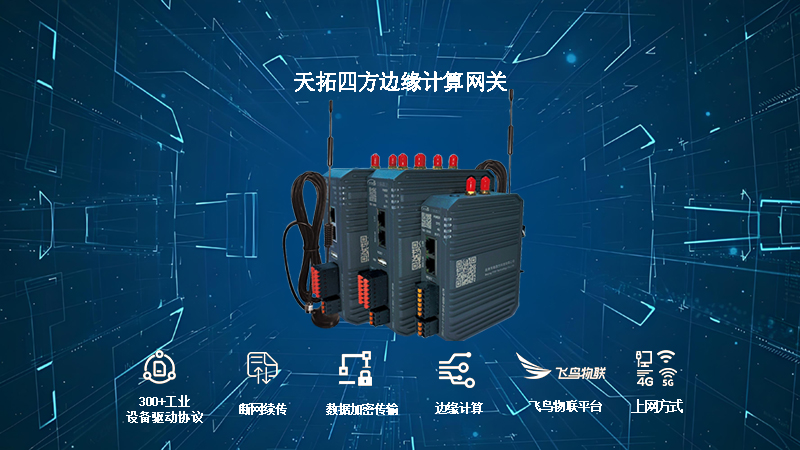
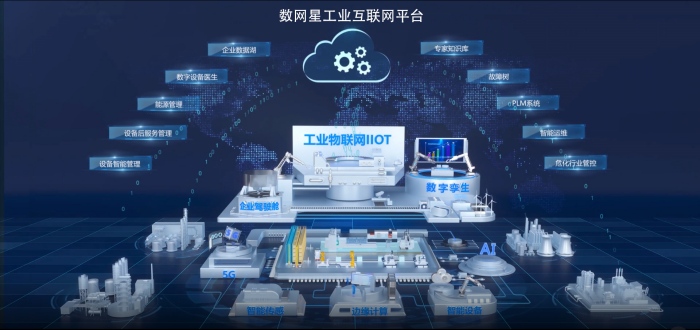
三、實(shí)施效果
通過實(shí)施車間設(shè)備數(shù)據(jù)采集系統(tǒng),該工廠取得了顯著的成效:
生產(chǎn)效率提高了20%,減少了生產(chǎn)瓶頸和等待時(shí)間。
設(shè)備故障率降低了30%,維護(hù)成本減少了15%。
產(chǎn)品質(zhì)量得到了有效提升,廢品率降低了10%。
能源消耗降低了15%,實(shí)現(xiàn)了節(jié)能減排的目標(biāo)。
車間設(shè)備數(shù)據(jù)采集是實(shí)現(xiàn)工廠數(shù)字化轉(zhuǎn)型的重要一步。通過采集、分析設(shè)備的運(yùn)行數(shù)據(jù),我們可以更好地了解設(shè)備的狀態(tài)和生產(chǎn)情況,從而優(yōu)化生產(chǎn)流程、提高生產(chǎn)效率、降低成本、保證產(chǎn)品質(zhì)量。